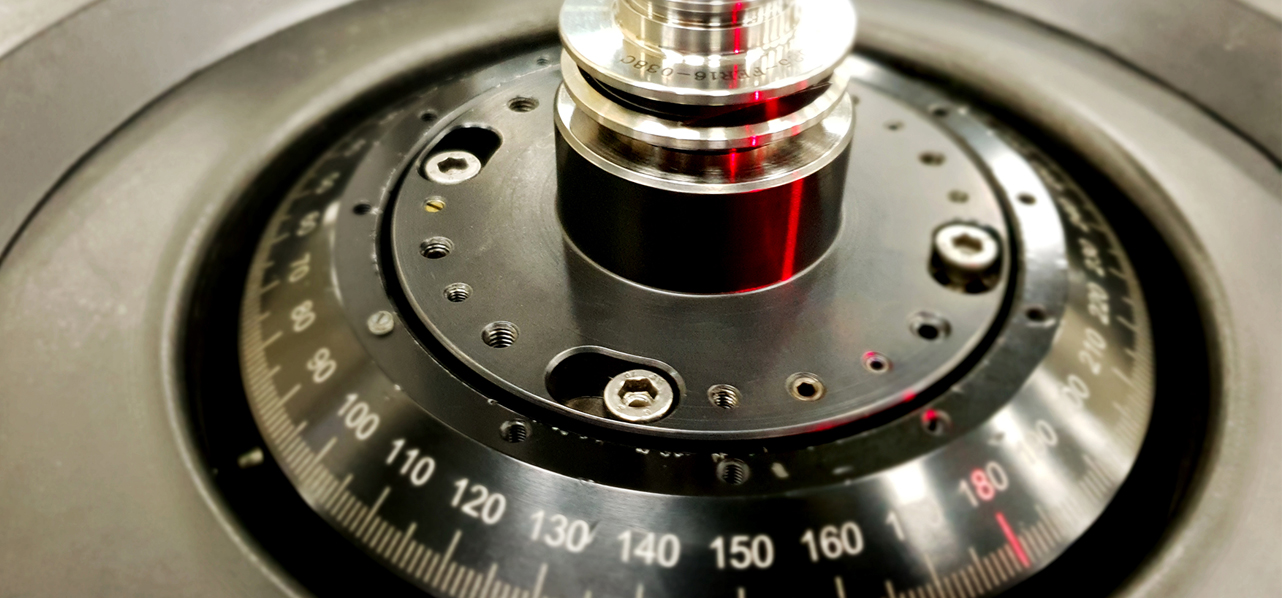
Balancing
Dynamic balance
In an environment where high-speed machines are becoming more and more popular, dynamic balance has been listed as the most basic index for a qualified tool holder along with the accuracy of the handle. The source of imbalance in the tool holder is usually functional, for example, it can be caused by the set screw in the end mill tool holder, or the unequal depth keyway in the CAT tool holder. These causes often appear randomly and there are no certain rules, so no matter what the situation, the user must eventually compensate for this imbalance in order to achieve the purpose of dynamic balance correction.
Generally speaking, all tool holders used for spindle speeds up to 8,000 revolutions need to be dynamically balanced. According to ANSI S 2.19, the dynamic balance grade can be divided into 11 grades from G 4,000 to G 0.4. The lower the G number, the higher the dynamic balance level. In addition, the allowable unbalance in dynamic balance is in g·mm or oz·mm. The calculation formula is as follows:
Uper = G/ω →Uper = 9549 x G x W / n
UperIs the allowable unbalance, G is the dynamic balance level, W is the weight of the knife, n is the speed
Assuming that the weight of the knife handle is W=1Kg, the dynamic balance level G6.3 is required, and at a speed of 15,000RPM,
The allowable balance is
9549 x 6.3 x 1 / 15,000=4.011 (g.mm)
The importance of dynamic balance
What we must pay attention to is that in a tool/toolholder device, the centrifugal force generated by the unbalanced state is proportional to the square of the spindle speed. In other words, a minute unbalance produced at 1 thousand revolutions per minute, the centrifugal force will increase 100 times at 10,000 revolutions, and 400 times at 20,000 revolutions. With the development trend of higher and higher spindle speeds, if the tool cannot keep rotating on the spindle centerline, it will become the main cause of additional imbalance. Therefore, good concentricity becomes more important. In the state of poor dynamic balance, the centrifugal force generated by the high-speed rotation of the spindle will cause preventable vibration or vibration. The effects of this vibration or vibration are as follows:
Machine spindle
The above-mentioned vibration or vibration will be transmitted to the spindle bearing, and once the bearing load exceeds the bearing load, it will cause temperature rise, thereby reducing the bearing life.
Tool life
The above-mentioned vibration or chatter will cause the tool to beat the workpiece to produce a variable cutting load, resulting in a significant reduction in tool life.
Workpiece
The above-mentioned vibration or vibration and the multiplied effect of the original clamping accuracy will cause the surface roughness of the processed workpiece to be poor and there are knife marks or the processing accuracy is greatly reduced.
Industrial safety
There are cases abroad that caused serious work safety problems due to high spindle speed and poor balance, which caused the tool holder to fly out and injured the machine operator.
The dynamic balance level of PARFAITE knife handle
Puhui is a company that produces high-quality technical products such as high-speed spindles, precision toolholders and special tools. Therefore, the manufacturing of high-speed spindles must reach the G0.4 dynamic balance level. According to this high-level demand, the dynamic balance of the toolholders is produced to achieve the quality and Customer's demand for dynamic balance. In terms of optimization, users need to perform dynamic balance correction actions after the tie rod, tool holder, collet, nut, and tool are combined to obtain the best dynamic balance effect. The dynamic balance of a single handle alone cannot guarantee the final dynamic balance level after the combination, because the tie rods, collets, nuts and tools themselves also have a certain degree of weight and contain imbalance. Finally, any replacement or adjustment of tools, replacement of any parts of the tool holder, grinding of tools... etc. may affect the original dynamic balance level. A good dynamic balance level can improve machining accuracy, extend tool life, reduce machine vibration, and increase spindle life. Its importance is especially visible.
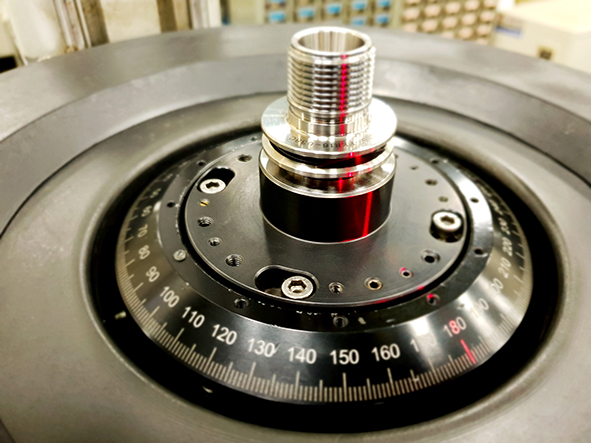