Balancing
Dynamic balance
The importance of clamping accuracy and repeatability is almost second only to handle accuracy or dynamic balance. Tool holder clamping accuracy refers to the deflection of the tool holder after clamping the tool. The measurement method is to rotate the test rod by 360 degrees at a position several times the length of the shank diameter after clamping the test rod and measure its deflection. As shown in the figure, the tool holder clamps the test rod and fixes it on the measuring tool. Using point A as the reference point, rotate 360 degrees to measure the deflection at point B or point C. The distance between the nose of the tool holder (point B) and point C is expressed as several times the tool holder diameter (assuming that the tool holder diameter O d is 6mm, and the 4 times length/4d is 24mm). The repeatability of the tool holder refers to the change in the clamping accuracy of each measurement under the condition of repeated disassembly or clamping of the tool holder. The longer the distance between point C, the more difficult it is to maintain the clamping accuracy and repeatability.
The importance of clamping accuracy and repeatability is almost second only to handle accuracy or dynamic balance. Tool holder clamping accuracy refers to the deflection of the tool holder after clamping the tool. The measurement method is to rotate the test rod by 360 degrees at a position several times the length of the shank diameter after clamping the test rod and measure its deflection. As shown in the figure, the tool holder clamps the test rod and fixes it on the measuring tool. Using point A as the reference point, rotate 360 degrees to measure the deflection at point B or point C. The distance between the nose of the tool holder (point B) and point C is expressed as several times the tool holder diameter (assuming that the tool holder diameter O d is 6mm, and the 4 times length/4d is 24mm). The repeatability of the tool holder refers to the change in the clamping accuracy of each measurement under the condition of repeated disassembly or clamping of the tool holder. The longer the distance between point C, the more difficult it is to maintain the clamping accuracy and repeatability.
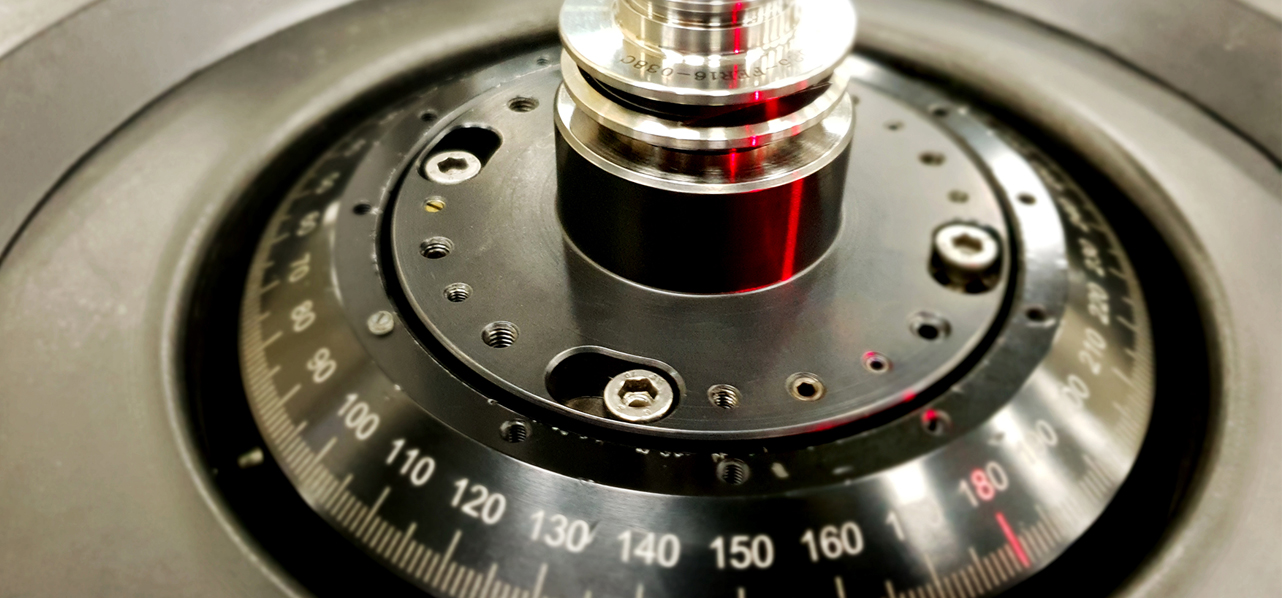