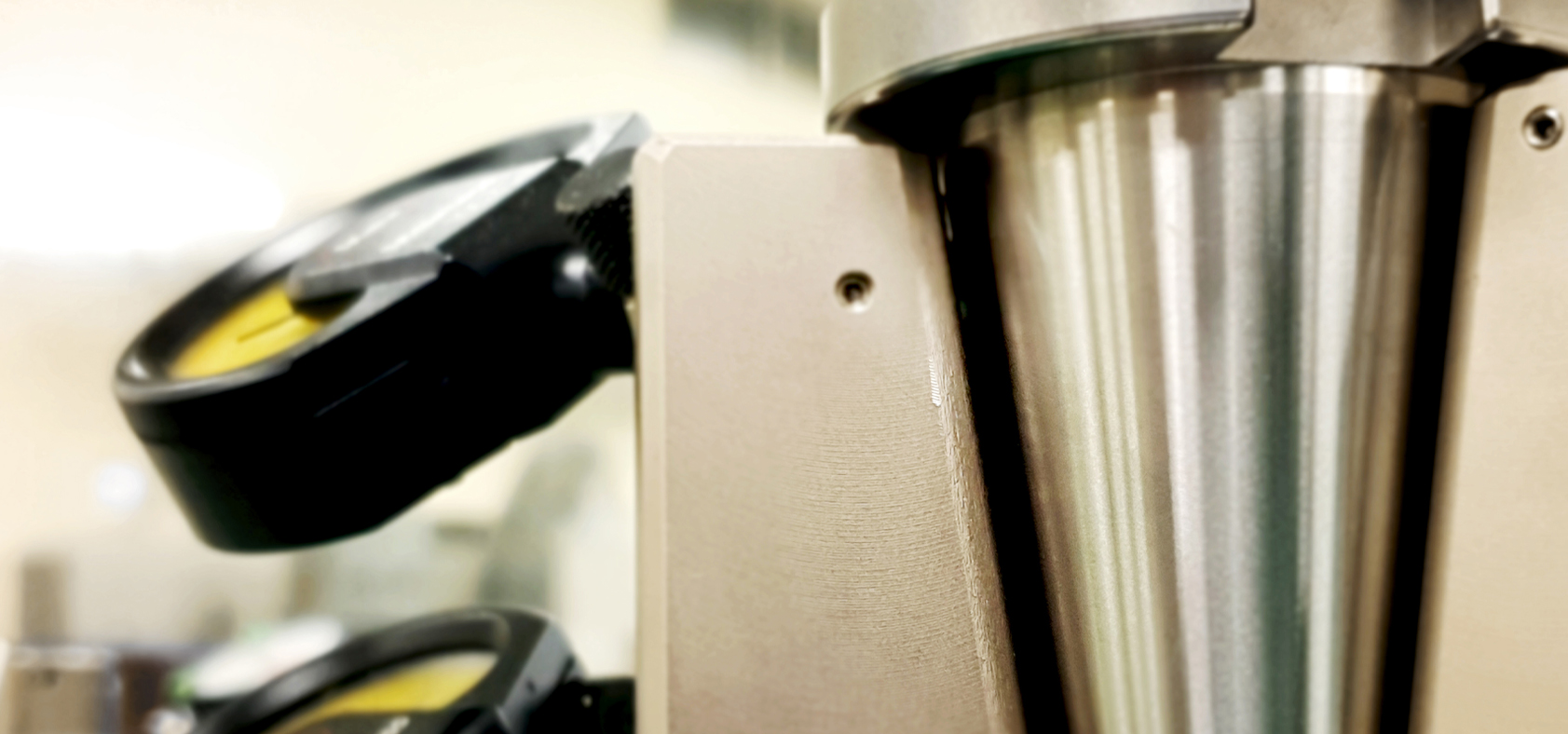
Taper Accuracy
Handle accuracy
Shank accuracy refers to the close tolerance of the shank of the tool holder and the inner hole of the spindle. This tolerance level is divided into 12 levels from AT 1 to AT 12. The higher the shank tolerance level, the closer the shank of the tool holder is to the inner hole of the spindle. For example, AT3, which has an area of 85%, is better than AT4. According to the standard recommendation of ISO1947, AT3 is the most basic requirement for the shank of a tool holder. For HSK tool holders, the German standard DIN 69893 clearly defines the tolerance range of all dimensions of HSK tool holders. This tolerance range is a fixed tolerance, so there is no distinction between tolerance levels. All of the above accuracy measurements must be measured with precise and regularly inspected measuring tools. Other methods such as applying red lead to the visual method, etc., cannot be accurately measured.
The importance of shank accuracy grade
Protect and extend the accuracy and life of the spindle
The higher the accuracy of the shank, the closer the shank is to the inner hole of the spindle, which means that the gap between the shank and the inner hole of the spindle will not continue to hit the inner hole of the spindle when the spindle is rotating. The impact is as minor as the damage, deformation, and poor accuracy of the spindle inner hole, and the worst is the spindle being scrapped. Especially in the high-speed machining environment, under the demand of expensive high-speed spindles with tens of thousands of revolutions, the importance of shank accuracy is very important. The accuracy of the shank exceeds the HSK tool holder of DIN 69893 standard. In the light of abnormal clamping and retraction, the long-term spindle accuracy is poor or damaged or deformed, and the accuracy of the spindle is lost and scrapped in the short term.
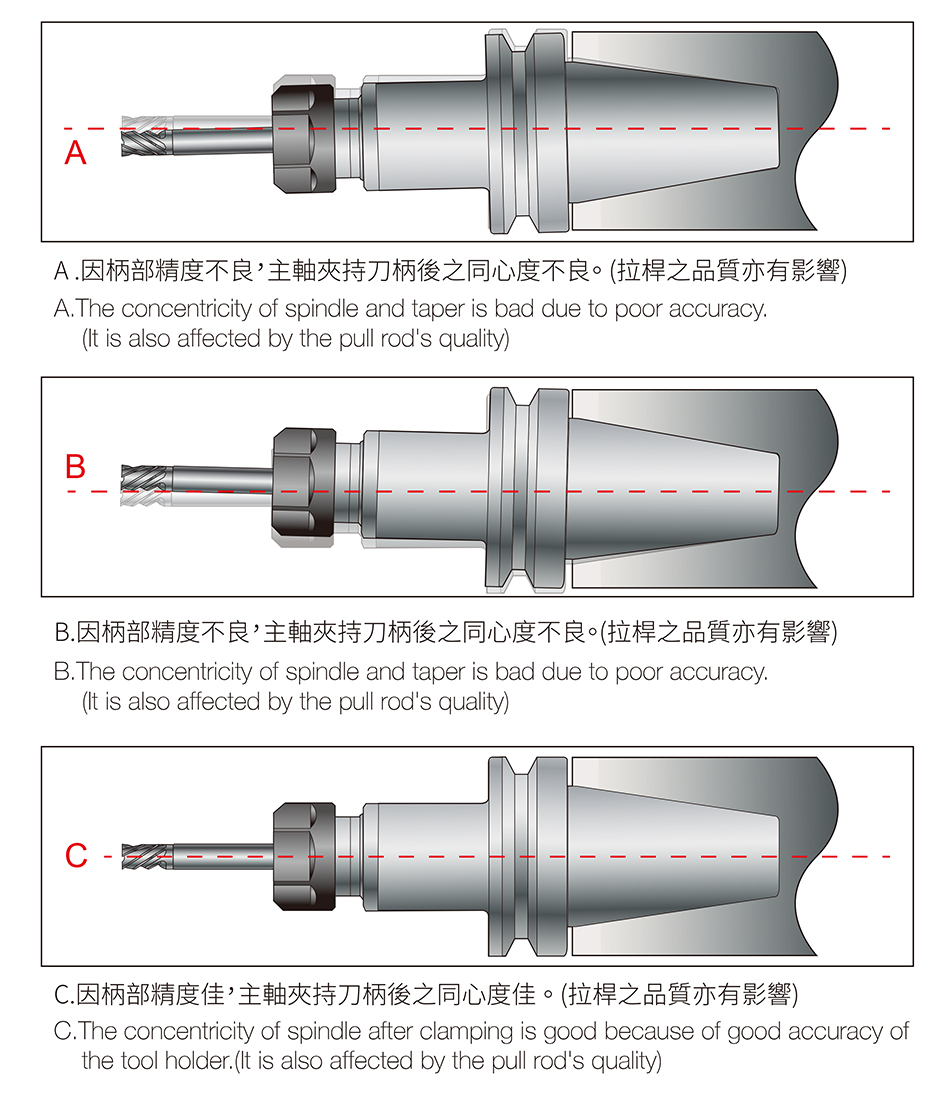
Protect and extend tool life
In theory, the higher the clamping accuracy, the longer the tool life. In practice, the deflection of the tool tip is largely due to the deviation caused by the excessive clearance between the tool holder and the spindle bore or the loss of accuracy of the spindle bore due to long-term use of tool holders with poor shank tolerances (as shown in the figure above) Shown). Therefore, the lower the accuracy of the shank, the worse the tool yaw, and the relatively poorer repeatability. In addition, the increase in defect rate and the increase in tool costs caused by rapid tool wear can no longer be ignored.
Ensure the accuracy and quality of the workpiece
In the same way, the accuracy of the shank is proportional to the deflection of the tool, so the accuracy and quality of the processed objects can also be guaranteed.
Precision grade of shank of PARFAITE shank
All the tool handles made by PARFAITE are guaranteed to fit over 85% or AT3. The tolerances of HSK tool holders are guaranteed to be manufactured in accordance with the tolerance range of DIN69893. The measuring instruments for the accuracy of the handle use precision measuring tools such as air gauges made in Germany and Switzerland and regularly checked and corrected.
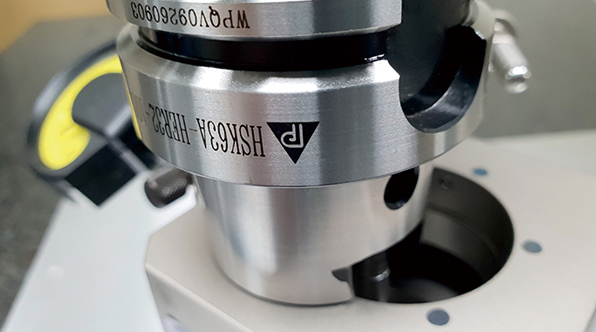